Robots in Warehousing: 2023 Top Players, Products and Advancements
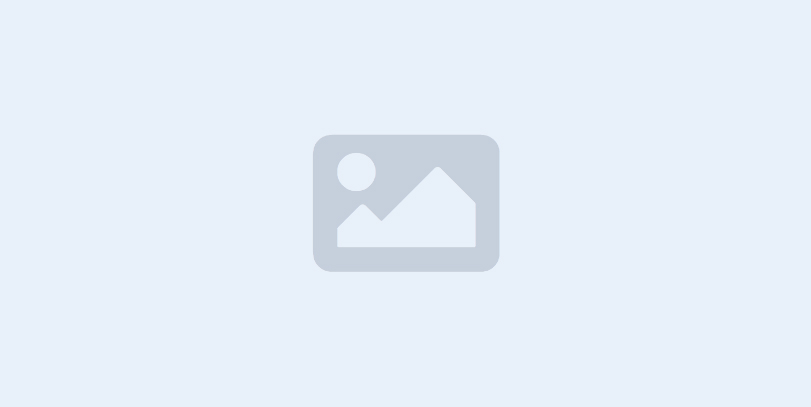
This News Covers
- Major investments and trends in Warehouse robots in 2023?
- Who are the top warehouse robot manufacturers?
- Which industrial challenges warehouse robots fulfill?
- What are some examples of Warehouse Robots?
- Are warehouse robots AI powered?
- Which companies have large fleets of warehouse robots?
Major investments and trends in Warehouse robots in 2023?
Warehouse automation trends in 2023:
- Key Drivers of Growth: The global warehouse automation market is estimated to grow at a CAGR of 14%, reaching a value of $30 billion by 2026. This growth is fueled by the boom in retail ecommerce, wage cost and flexibility, and technological leaps.
- Ecommerce and Rapid Fulfillment: The shift from brick-and-mortar shopping to online shopping is driving the need for modern fulfillment and shipping practices. Rapid order fulfillment is becoming a necessity, and warehouses are investing in automation to meet these demands.
- Wage Cost and Flexibility: Rising wage rates in regions like Europe and North America are reducing company profit margins. Investing in warehouse automation to replace labor is seen as cost-effective with high ROI. Automated warehouses can easily handle order spikes during peak holiday seasons, which manual warehouses struggle with.
- Technological Leaps: Rapid technological development in robotics, mechanics, machine vision, AI, and deep learning is driving growth in warehouse automation. The emergence of the Industrial Internet of Things (IIoT) and completely connected warehouse systems are further driving this growth.
- Rise of the Robots: The market for mobile robots is expected to rise by over $334 billion between 2032 and 2042. Robots are being used for a wide range of tasks in warehouses, such as sorting, picking, packaging, batching, transportation, fulfillment, security, and inspection. Amazon leads the way in robot-driven warehouses with over 200,000 mobile robots implemented in its facilities.
- Mobile Robots (AGV/AMR): Automated Guided Vehicles (AGV) and Automated Mobile Robots (AMRs) are becoming popular in warehouse automation. They are scalable and don't require changes to the warehouse's existing floor plan and infrastructure. The global AGV/AMR market size will reach more than $18 billion by 2027.
Who are the top Warehouse Robot Manufacturers?
Here are the top warehouse robotics companies.
- ABB: A Swedish-Swiss multinational corporation headquartered in Switzerland, ABB operates primarily in robotics, power, heavy electrical equipment, and automation technology areas. It is known as one of the leading warehouse robotics companies.
- KUKA: A German company that manufactures robots and systems for factory automation. KUKA is a leading global provider of intelligent automation solutions, offering everything from robots and cells to fully automated systems and their networking in markets such as healthcare, electronics, consumer goods, and the general industry.
- Yaskawa: A Japanese company that manufactures servos, motor drives, switches, AC motor controllers, and industrial robots. They manufacture Motoman heavy-duty industrial robots that can be used in welding, packaging, assembly, coating, cutting, material handling, and general automation.
- Fetch Robotics: A US-based company, Fetch Robotics is the pioneer of on-demand automation. The company provides the warehousing and intralogistics industry with safe, reliable, and versatile autonomous mobile robots.
- Honeywell: An American publicly traded multinational conglomerate corporation, Honeywell operates in four major areas: aerospace, building technologies, performance materials and technologies, and safety and productivity solutions.
- Omron: A Japanese electronics manufacturer, Omron has been innovating products for all types of industries and is known as one of the best warehouse robotics companies.
- Daifuku: A Japanese company that specializes in material handling equipment. Daifuku is currently the world's largest material handling system provider.
In addition to these, the four largest manufacturers of industrial robots globally are Fanuc and Yaskawa of Japan, KUKA of Germany, and ABB of Switzerland. These companies command around three-quarters of the global market.
Which industrial challenges warehouse robots fulfill?
Here are the industrial challenges that warehouse robots help to fulfill:
- Navigation in Dynamic Environments: Warehouses are constantly changing due to the movement of products and shifting walls of boxes. Robots equipped with advanced vision tools and software can recognize their surroundings well enough to properly function and adapt to these changes.
- Adapting to New Variables and Obstacles: Warehouses are dynamic environments where people, crates, pallets, etc., appear in aisles frequently and without warning, presenting numerous obstacles for robots to navigate. Additionally, items are often placed in a haphazard, unorganized way, and there's no guarantee that an item is undamaged or in the correct place. New SKUs come in all the time with a wide variety of shapes, sizes, and weights, all of which present new variables that robots must learn and adapt to.
- Item Manipulation: Getting an item off the shelf and to a box is a major technical obstacle for robots. Various robots have attempted to deal with the dynamic nature of items, but all have lacked a robust, adaptive robotic system that is designed to handle the day-to-day challenges of item manipulation. Creating a robotic arm capable of handling a large variety of item sizes is very challenging, especially with cost constraints in mind.
- Costs and ROI: The total cost of implementing robotic solutions must be less than the productivity and efficiency gained by adding them to existing systems and labor. Otherwise, a warehouse has shiny new toys but becomes less competitive. Existing solutions have been extremely cost-prohibitive to many warehouses, often requiring a huge upfront commitment to handle even average amounts of throughput and only achieving a ROI after more than five years.
- Rigidity: Some outdated systems can't be updated or disassembled once installed.
- Customization: In the past, automation lacked standardization. For a fully-developed system, it could take up to a year for deployment.
- Scalability: After you've made an investment, the solution you choose may not be scalable.
- Integration: Ideally, you would want any automation solution to integrate with your existing systems, but not all of them will do this.
- Service: Some automation tools require frequent and costly maintenance and service.
These challenges are being addressed by the development of adaptive robots that can operate within a constantly shifting environment without frequent reprogramming. These robots maneuver around navigation and manipulation roadblocks with their advanced vision tools and software that enables picking precision, all with lower cost hardware platforms.
What are some examples of Warehouse Robots?
Here are some examples of warehouse robots that have been highlighted in 2023:
- Automated Guided Vehicles (AGVs): These are some of the most effective and innovative solutions for increasing productivity and improving safety in warehouses requiring pallet handling activities. Self-driving forklifts can manage different types of material handling solutions like racking, drive-in, gravity, block stacking, etc.
- Autonomous Mobile Robots (AMRs): Autonomous self-navigating robots can move around a warehouse, pick up and move objects, and perform other tasks. AMR robots aim to enhance pickers' efficiency and productivity by replacing traditional fulfillment solutions that required tons of wasted time.
- Palletizer Robots: These use advanced end-of-arm tooling (EOAT) to pick up items and position them on pallets in the correct pattern, decreasing the need for manual labor and enhancing efficiency.
- Depalletizing Robots: Robotic depalletizing has completely changed how pallets are unloaded in technologically advanced warehouses and distribution centers. These technologies provide rapid, efficient, and precise pallet unloading, improving productivity and lowering labor expenses.
- Conveyor Systems: Conveyors are an important part of contemporary warehouses and distribution centers because they provide a quick and effective means to transfer items and materials from one area to another.
- Automated Storage and Retrieval Systems (ASRS): An ASRS or automated storage and retrieval system uses software, computers, and robots to automate warehouse handling, storage, and retrieval.
- Sorting Robots: These high-tech systems can combine robotics, conveyors, carousels, and vision-guided technologies, opening up unlimited options for optimizing warehouse operations and increasing efficiency.
- Packing Robots: Packing robots are used in warehouses and distribution centers to automate the process of packaging items into containers such as boxes, bags, or envelopes.
- Pick and Place Robots: These robots are frequently outfitted with sensors and vision systems in order to move goods from or to a moving conveyor belt.
- Inventory Robots: Warehouse and distribution facilities can benefit greatly from the employment of inventory robots, which were developed to automate the arduous task of inventory management.
- Cleaning Robots: Cleaning robots can help keep warehouses cleaner and safer for employees by eliminating germs and other impurities that could cause disease.
- Security Robots: To enhance safety and security, mobile security robots are increasingly being implemented in warehouses.
- Drones: Unmanned Aerial Vehicles (UAVs) or drones have several applications in warehouses. Some uses for drones in storage facilities include the following: drones equipped with cameras or sensors may be flown above warehouse shelves to take pictures of the items there.
- Automated Labeling Robots: Warehouses and distribution hubs utilize automatic labeling robots to label items. Sensors and cameras help the robot place the label in the right spot on the product or packaging.
- Case Erectors: At warehouses and packing facilities, case erectors mechanically build cardboard boxes and cases from flat folded cardboard.
- Automated Stretch Wrappers: Robots known as automated stretch wrappers are commonly seen at distribution centers and warehouses where they are employed to wrap pallets of items in stretch film to keep them safe while in transit or storage.
Are warehouse robots AI powered?
Warehouse robots are indeed powered by Artificial Intelligence (AI). The integration of AI into warehouse robotics has revolutionized the industry by enhancing the capabilities of these machines and enabling them to perform tasks that were previously impossible to automate. The key areas where AI has significantly impacted warehouse robotics are:
1. Enhanced Learning and Adaptability:
AI-enabled robotics can help robots learn like humans, which could have a massive impact on how traditional manufacturing operates. Robots are inflexible by design, but AI-enabled robotics that use sensors, data-driven computation, and more can enhance their capabilities. The combination of artificial intelligence (AI), machine learning (ML), deep learning (DL), and robotics are beginning to transition to industrial manufacturing facilities. These advanced robotic systems enable the automation of industrial processes that were impossible to automate up until now.
2. Improved Perception and Computation
AI allows robots to perceive their environment using sensors, cameras, torque sensors, tactile sensing, and similar feedback. Data-driven computation situations need to be processed to something meaningful so the robot can compute the observation. Augmenting a robot arm with tooling is a lot of what makes robots hard, but the action and the process can be made easier by using sensor and computation technology and integrating the automation systems.
3. Democratization of AI-Enabled Robotics:
The barriers to AI-enabled robotics won't come down until the technology becomes readily available. The democratization of AI-enabled robotics technology by encapsulating solutions for complex tasks in easy-to-use software will help make robotics more accessible. They need to be offered in a way so they can be used for automation engineers in the field and not just the few experts.
AI has the potential to transform the warehouse industry by making robots smarter, more efficient, and more adaptable. With further advances in machine learning and reduced hardware costs, we can expect to see more applications of AI in warehouse robotics in the future.
Give list of 5 product names in warehouse robots?
Here are five examples of warehouse robot products:
- Ella Smart Stroller GlüxKind: This is a smart travel system that comes with a variety of AI-powered features. Although not a warehouse robot, it represents the kind of AI-powered automation that is also being applied in the warehouse industry.
- DEMATIC: This was the world's largest warehouse automation provider in 2021. It is part of KION Supply Chain Solutions.
- Amazon Picker Robot: This new Amazon robot can handle 1,000 items per hour, bringing the company closer to fully automating their warehouses.
- ABB Robotics Products: ABB's portfolio of robotics products serves several industries, including healthcare, logistics, metal fabrication, construction, and fabrication.
- Ottobot Yeti: Ottonomy demoed the new Ottobot Yeti last-mile delivery robot at CES 2023. This new platform includes an entirely new drive platform that includes holonomic motion using a four-wheel swerve drive. The cargo-carrying payload platform has also been redesigned to be larger and more robust.
Which companies have large fleets of warehouse robots?
Here are some companies that have large or the largest fleets of warehouse robots or regularly purchase warehouse robots in large numbers:
- Amazon: Amazon currently has more than 750,000 mobile drive units nicknamed Hercules, which were originally Kiva Robotics robots. Additionally, they have deployed more than 1,000 Robin robotic arms and recently added Proteus, an autonomous mobile drive unit designed to work safely alongside humans on the warehouse floor.
- Alibaba: Alibaba, the Chinese e-commerce giant, has also invested significantly in warehouse automation. The company's warehouses are known for their extensive use of robots, which are used for tasks such as picking, packing, and sorting. Alibaba has partnered with various robotics companies to enhance its warehouse operations.
- Walmart: Walmart has been investing in warehouse automation to improve efficiency and reduce costs. The company uses autonomous mobile robots (AMRs) for tasks such as sorting items and moving goods around its warehouses.
- DHL: DHL, one of the world's largest logistics companies, has been investing in warehouse automation to improve efficiency and accuracy in its operations. The company uses robots for tasks such as picking and packing, as well as for sorting and moving goods.
- FedEx: FedEx has been investing in warehouse automation to improve its operations. The company uses robots for various tasks, including sorting packages and moving goods around its warehouses.
What are the costs of warehouse robots?
The cost of a warehouse robot depends on the type and size of the operation. For the Kiva robots, a "startup kit" with robots costs between $1 million to $2 million. For a larger warehouse operation needing up to 1,000 robots, the cost ranges from $15 to $20 million. However, it's worth noting that the average price of industrial robots, including warehouse robots, is expected to decrease significantly over time. By 2025, the price is forecasted to dip to less than $10,900 per robot due to lower technology costs.
Here are some factors that can influence the cost of warehouse robots:
- Type of Robot: The cost can vary based on whether the robot is an Automated Guided Vehicle (AGV), Autonomous Mobile Robot (AMR), or a stationary robot like a robotic arm. AGVs and AMRs, which can navigate autonomously around the warehouse, tend to be more expensive than stationary robots.
- Capabilities: Robots with advanced capabilities like picking and packing, sorting, and more complex tasks will be more expensive than robots designed for simpler tasks like moving goods from one place to another.
- Payload Capacity: Robots designed to carry heavier loads will generally be more expensive than those with a lower payload capacity.
- Integration Costs: The cost of integrating the robots into existing warehouse systems can also add to the overall cost. This can include software integration, training for staff, and potential modifications to the warehouse layout.
- Maintenance and Upgrades: Ongoing costs for maintenance and potential upgrades can also factor into the total cost of ownership for warehouse robots.
GET AHEAD
Top Research Reports to Fuel Your Industry Knowledge- Autonomous Mobile Robots (AMR) Market by Navigation Technology (Laser/LiDAR, Vision Guidance, SLAM, RFID Tags, Magnetic & Inertial Sensors), Batteries, Sensors, Actuators, Payload Capacity (<100 kg, 100–500 kg and >500 kg) – Global Forecast to 2030
- Surgical Robots Market by Product (Instruments & Accessories, Systems, Services), Application (Urological Surgery, Gynecological Surgery, Orthopedic Surgery, Neurosurgery), End User (Hospitals, Ambulatory Surgery Centers) & Region - Global Forecast to 2029
- Delivery Robots Market Size, Share, Statistics and Industry Growth Analysis Report by Offering (Hardware, Software), Load Carrying Capacity, Number of Wheels (3 wheels, 4 wheels, 6 wheels), Speed Limit, End-user Industry (Food & Beverage, Retail, Healthcare, Postal) and Region - Global Forecast to 2028
Editor's Pick

Healthcare
MiniMed™ 780G & Simplera Sync™: Smarter Tech, Simpler Lives for Diabetes Patients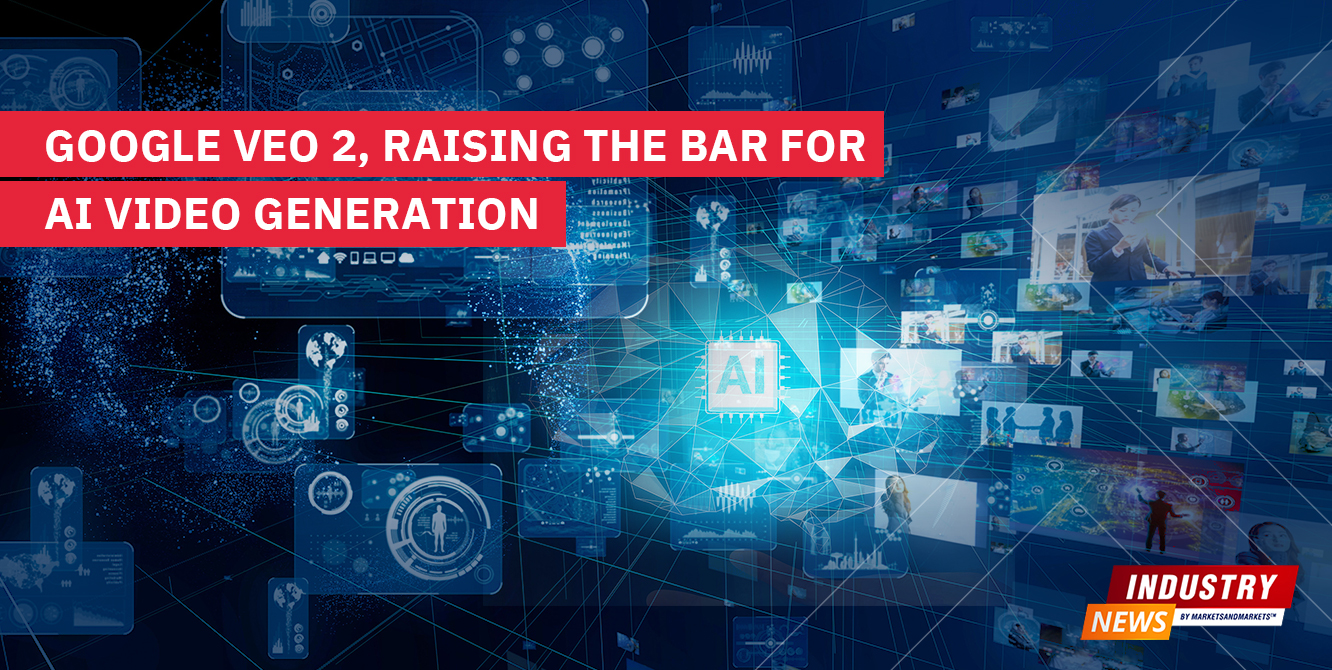
Information and Communication Technology
Google Veo 2, Raising the Bar for AI Video Generation.jpg)
Automotive & Transportation
Trump’s Reciprocal Tariffs Stir Ripples Across the Automotive IndustryPODCASTS
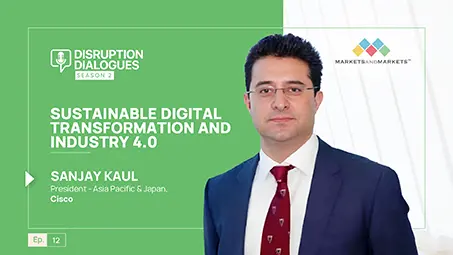
Sustainable Digital Transformation & Industry 4.0
Sanjay Kaul, President-Asia Pacific & Japan, Cisco, and host Aashish Mehra, Chief Research Officer, MarketsandMarkets, in conversation on unraveling 'Sustainable Digital Transformation and Industry 4.0'
11 July 2023|S2E12|Listen Now
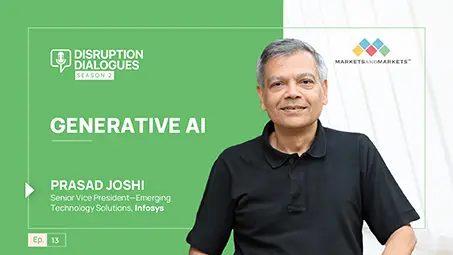
Generative AI
Prasad Joshi, Senior Vice President-Emerging Technology Solutions, Infosys, and host, Vinod Chikkareddy, CCO, MarketsandMarkets, in exploring the recent advances in AI and the generative AI space.
7 Nov 2023|S2E13|Listen Now
Download Whitepaper
