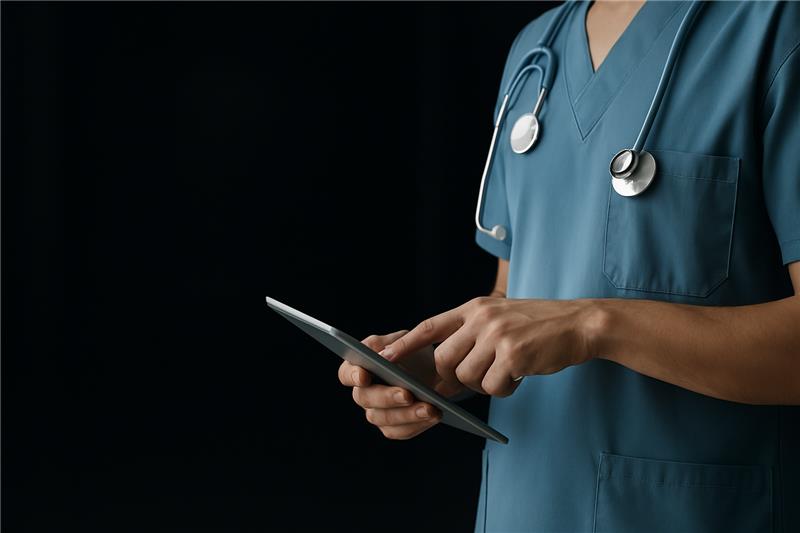
Single-Use Bioreactors: Transforming Biopharmaceutical Manufacturing
Single-use bioreactors (SUBs) have emerged as a transformative solution in biopharmaceutical manufacturing, offering enhanced flexibility, efficiency, and cost-effectiveness. By replacing traditional stainless steel or glass vessels with disposable plastic bags, SUBs streamline operations and reduce the complexities associated with cleaning and sterilization. This shift is particularly advantageous in environments requiring rapid changeovers and stringent contamination controls.?
Understanding Single-Use Bioreactors
At their core, single-use bioreactors utilize a disposable plastic bag as the culture vessel, encased within a supportive structure such as a rocker or cylindrical frame. These bags are typically constructed from multi-layered plastic films designed to provide mechanical stability, gas impermeability, and biocompatibility. Common materials include polyethylene terephthalate (PET), low-density polyethylene (LDPE), polyvinyl alcohol (PVA), polyvinyl chloride (PVC), and polypropylene (PP). For medical applications, materials in contact with the product must meet regulatory standards set by authorities like the European Medicines Agency.
Types of Single-Use Bioreactors
SUBs are primarily categorized based on their agitation mechanisms:?
- Stirred-Tank SUBs: These systems incorporate integrated stirrers within the disposable bag, connected to external drivers either mechanically or magnetically. The entire assembly is pre-sterilized, facilitating immediate use upon installation.?
- Rocking Motion SUBs: Utilizing a rocking platform, these bioreactors agitate the culture medium without internal mechanical components. This design simplifies the system and reduces potential contamination points.?
Both types are available in volumes up to approximately 1,000 liters, with some manufacturers offering systems up to 2,000 liters to accommodate larger-scale production needs.?
Measurement and Control Challenges
Monitoring and controlling culture conditions in SUBs present unique challenges due to their closed, pre-sterilized nature. Traditional sensors cannot be inserted post-sterilization; therefore, measurement devices must be integrated during manufacturing. Innovations such as optical sensors and pH-sensitive patches have been developed to enable non-invasive monitoring of critical parameters like pH, temperature, and dissolved oxygen. These technologies allow for real-time data acquisition without compromising the sterile environment.?
Advantages of Single-Use Bioreactors
SUBs offer several compelling benefits over conventional systems:?
- Reduced Cleaning and Sterilization: Eliminating the need for cleaning and sterilization between batches significantly decreases downtime and resource consumption.?
- Lower Cross-Contamination Risk: The disposable nature of the culture vessel minimizes the potential for cross-contamination, enhancing product safety.?
- Operational Flexibility: SUBs enable rapid changeovers between different products, making them ideal for facilities handling multiple therapies or frequent process modifications.
- Cost Efficiency: By reducing the need for cleaning validation and associated utilities, SUBs can lead to substantial cost savings, particularly in multi-product facilities.?
- Scalability: With systems ranging from bench-top to production-scale, SUBs facilitate seamless scale-up from development to manufacturing.?
Limitations and Considerations
Despite their advantages, SUBs have certain limitations:?
- Oxygen Transfer Limitations: The design constraints of disposable bags can limit oxygen transfer rates, potentially affecting high-density cultures.?
- Shear Sensitivity: The gentle mixing required to protect delicate cells may not be sufficient for all applications, necessitating careful process optimization.?
- Waste Generation: The single-use nature of these systems contributes to increased plastic waste, raising environmental concerns.?
- Sensor Integration: The need for pre-installed sensors limits flexibility and may increase costs.?
Environmental Impact
The environmental footprint of SUBs is a topic of ongoing discussion. While they reduce water and energy usage associated with cleaning and sterilization, they generate additional plastic waste. Life cycle assessments suggest that, overall, SUBs may offer environmental benefits by decreasing resource consumption, but waste management strategies are essential to mitigate their impact.?
Market Outlook
As per the report published by MarketsandMarkets, The global single-use bioreactors market, valued at US$4.1 billion in 2023, is forecasted to grow at a robust CAGR of 15.4%, reaching US$4.4 billion in 2024 and an impressive US$9.1 billion by 2029.
Conclusion
Single-use bioreactors represent a significant advancement in biopharmaceutical manufacturing, offering enhanced flexibility, efficiency, and safety. While they present certain challenges, ongoing innovations continue to expand their applicability and performance. As the industry evolves, SUBs are poised to play a pivotal role in meeting the demands of modern bioprocessing.?
80% of the Forbes Global 2000 B2B companies rely on MarketsandMarkets to identify growth opportunities in emerging technologies and use cases that will have a positive revenue impact.
- Leading Automated Guided Vehicle Companies 2024: An In-depth Analysis
- CHARGED UP: SHIFT TO E-MOBILITY AND THE EVOLUTION OF TRANSPORTATION
- Global Automotive Market: Predictions For 2024
- Revolutionizing Depot Charging: Hockey Stick Growth on the Cards
- The Future of Silicon Battery Industry: Innovations and Market Outlook
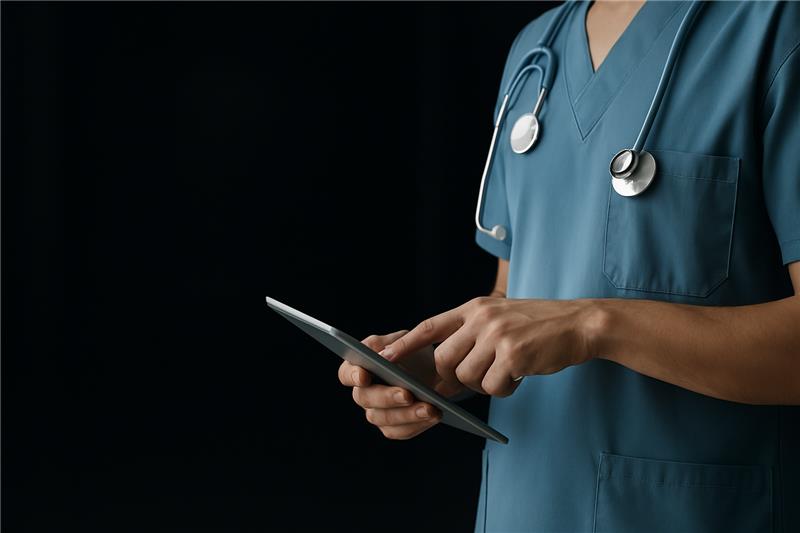
